During air conditioning maintenance a technician will inspect and clean components to ensure that they are functioning properly. If the technician finds a component that needs repair then the service professional will make that repair. Contact Air Conditioning Repair Round Rock TX for professional help.
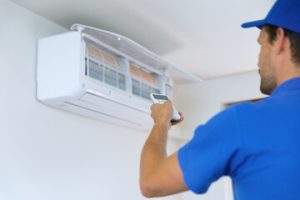
Occasionally, experienced DIYers can perform some basic air conditioner repair tasks such as cleaning the condenser and evaporator coils or clearing the refrigerant line. Learn how to troubleshoot some common AC problems that can be repaired yourself and save yourself the cost of calling a professional.
An evaporator coil that becomes clogged or dirty prevents the AC from absorbing enough heat to cool the air. This can also cause the system to short cycle more often, meaning it turns on and off more than necessary. This wastes energy and accelerates wear and tear on the system’s major components.
The first step to diagnosing this problem is turning off the system and locating the coils. They will be housed inside the air handler and located near the blower fan. It may be helpful to consult the owner’s manual if you have difficulty locating them. Before attempting to clean the coils, make sure you have all your safety gear in place and are familiar with the process.
Once the coils are clogged, they will freeze over and halt airflow to the system. To avoid further damage, you will need to turn the unit off and wait until the ice thaws, which usually takes several hours. During this time, it’s a good idea to have some containers on hand to catch the water that will drip from the coil as it thaws.
When the ice melts, it will drip down the coil and into a drain line. Over time, the dirt in the dripping water will build up and create a clog that will cause the drain to overflow. This can lead to high humidity, moldy odors, and serious health hazards from toxic mold spores. To avoid this issue, homeowners should regularly clean the air filter and inspect the drain line for clogs. Air conditioning service experts can offer maintenance programs that guarantee cleaning of the coils to prevent this problem. They can also clean the aluminum fins to keep them from becoming bent, which reduces airflow and efficiency.
Dirty Compressor Coils
Dirty compressor coils also reduce the ability of your AC system to absorb and dump heat effectively, which makes it harder for your home to reach your preferred temperature. This causes your system to work longer and harder than it should, adding to the overall wear and tear on other components that can eventually lead to a costly air conditioning repair.
You’ll know when your air conditioner needs its coils cleaned if you’re paying close attention to your energy bills. Increasing utility bills are an obvious sign that your AC system is working longer and harder to meet your cooling demands.
In addition to higher energy bills, dirty coils can affect your home’s value and make it harder to sell if you decide to move. Moreover, a dirty coil will reduce your energy efficiency rating and may even prevent you from qualifying for certain tax reductions or benefits that depend on a high home energy efficiency rating.
Your dealer will shut off the power to your outdoor unit and remove the outer cover, allowing you to see the coils. They’ll start by blowing off loose dirt and debris with a shop vac or a soft brush, then using a noncaustic and nonfuming coil cleaner to thoroughly clean them. They’ll spray the cleaner on and rinse it off, making sure to follow the manufacturer’s instructions. They’ll also straighten bent fins if necessary.
If you’re concerned about the cleanliness of your air conditioner coils, it’s a good idea to have them cleaned twice each year. Your dealer can help you decide if this is a good option for your system and recommend the right cleaning method.
Low Coolant Levels
Engine coolant — a mixture of antifreeze and water — helps to pull heat away from the engine as it operates, helping to prevent overheating. Without enough coolant, temperatures under the hood can quickly rise, leading to damage including warped cylinder heads and a blown head gasket that requires expensive repairs.
While some loss of coolant from the reservoir is natural, constant evaporation or leaks from hoses and other components can reduce levels to unsafe levels. Insufficient coolant can also lead to the heater not working correctly, as it needs sufficient coolant to work. Other warning signs of low coolant include a rising temperature gauge, a sweet smell (due to the leaking antifreeze), and reduced fuel efficiency.
The main reason to avoid driving with low engine coolant is that overheating can cause severe and irreparable damage, requiring costly mechanical repairs or even a replacement engine. Coolant is designed to absorb and disperse heat from the engine, so if there isn’t enough of it in the cooling system, the temperature under the hood can rise quickly.
Aside from overheating, other issues that can occur with low engine coolant include a blown head gasket, warped cylinder heads and faulty valves. The cylinder heads are responsible for sealing the combustion chamber, so when they crack from excess heat, they can allow oil to enter the combustion process and cause damage. Additionally, if the coolant is not properly flowing through the system, the water pump can lose lubrication, increasing the risk of failure. The best way to protect against these problems is with regular inspections and maintenance by a professional service. These services can identify potential problems before they become serious and costly.
Failed Contactor
The contactor is an important electrical component that controls the flow of electricity to the compressor. If the contactor wears out, it can lead to a variety of issues. Identifying the issue can help you avoid expensive repairs. A constant clicking noise is a common sign that the contactor is not engaging properly. This can put unnecessary strain on the system, leading to premature wear and tear of other components.
A faulty contactor can also cause your AC unit to short-cycle. A short-cycle is a cycle that occurs when the air conditioner turns on and off repeatedly. This can be frustrating because it will not cool your home effectively.
If you suspect that your contactor is faulty, you should contact a professional HVAC technician for an inspection. They can replace the contactor and restore normal cooling.
Faulty contactors are usually caused by repeated voltage influxes. This can lead to pitting and arcing. If the contactor is not properly sealed, it can weld together and prevent the flow of electricity to the air conditioning system. Other signs of a faulty contactor include a humming sound and an inability to turn the AC off.
To test your AC contactor, shut off the power to your unit. Once the power is off, remove the side cover of the condenser. You will see a number of colorful wires connected to a black rectangle that is positioned vertically. The black rectangle is your air conditioning contactor. Take pictures of the wires and the contactor so you can easily reconnect them when replacing it. Next, use a multimeter to check for continuity between the volt terminals on each side of the contactor.
Failed Blower Motor
As time goes by, your blower motor may start to show signs of wear and tear. Eventually, it won’t be able to keep up with airflow requirements, leading to weak or no airflow through the vents. This is often the first sign of a failing blower motor and it will require an immediate replacement or repair.
Other signs of a failing blower motor include unusual noises such as screeching or squealing. This can indicate loose bearings or other mechanical problems, as well as a burning smell that points to overheating or electrical problems.
A failing blower motor can also lead to intermittent problems such as the fan only operating at certain speeds or the fan never turning on at all. These are more serious issues that should be checked out by a professional to rule out other problems such as a bad thermostat or relay.
Some blower motors use a resistor pack to control speed, while others are equipped with a control module that uses electronics to regulate speed based on sensor input. A resistor pack can fail due to overheating and corrosion, while a control module will need to be diagnosed using a scan tool or multimeter.
Loose or disconnected wiring can also cause blower motor failure, as well as overheating and electrical problems. Some can be fixed by simply reconnecting them or resoldering them, while others will require the use of a multimeter or a wire harness tester to check for power and voltage output. A visual inspection can also reveal any frayed or corroded cables or connectors that need to be replaced.